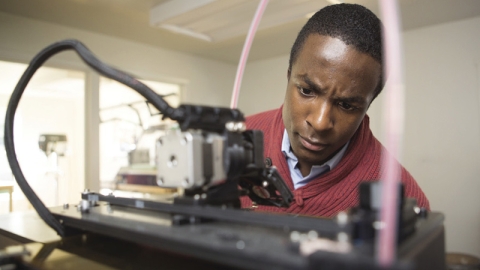
Bucknell in 3-D
January 19, 2016
Jemuel Stephenson '17, a student worker at the 7th Street Studio who wrote a patent for a 3-D printer, checks a print’s progress.
The magic of the maker movement takes hold in many innovative pockets on campus.
There is something enchanting about watching a 3-D printer in action and it’s even more enthralling if you’re behind the controls. Download a file from the internet or design one yourself, press print and watch the image on your screen begin to materialize point-by-point in plastic — it’s hard not to crack a smile.
"For most people it starts as something that impresses them because they’ve done it — it’s not the thing they’ve made; it’s just that there is a thing when there wasn’t one before," says Margot Vigeant, associate dean of engineering and a professor of chemical engineering. "A lot of people will make something out of a video game or movies: 'Look, it’s Darth Vader! I made him!' "
It’s a bit gimmicky, perhaps, but that feeling of wonder and agency is nonetheless powerful and it can be a transformational experience, says Vigeant. It’s one she and other leaders of the maker movement burgeoning at Bucknell and nationally hope to capture for all it’s worth, because putting the magic in your hands demystifies the trick; it makes you the magician.
That feeling is one the engineers and artists on campus, like Sam Pratt ’16, a mechanical engineering major, already know well. Pratt has been building 3-D printers since his senior year of high school and understands the mechanical minutia of the technology as well as anyone at Bucknell, but talk to him about that tech and it doesn’t take long for him to mention "magic."
"I had a part break on my printer and I emailed someone at the company and asked them for a file," Pratt says. "They emailed it to me and I printed the replacement part — like a 3-D fax machine. That’s like magic."
To Vigeant, a better term is "self-efficacy. You go from thinking this is something that’s not an option to, 'I can.' That’s inspirational."
It’s a feeling that can benefit anyone, Vigeant says and it’s the idea driving the maker movement — a tech-savvy extension of do-it-yourself culture supported at Bucknell by six facilities branded MakerSpaces, the 7th Street Studio among them.
Renovated in 2015 and outfitted with four 3-D printers (as well as three 3-D scanners, a laser cutter, a computer-numerical-control mill and design software to make it all go), the space provides training for any student, staff member or professor to try new ways of designing and crafting objects.
"You get people interested in making things, then they want to learn how to do it better," says Professor Nate Siegel, mechanical engineering, who manages the studio with Art Professor Joe Meiser and 7th Street Studio Coordinator Gretchen Heuges. "It allows people to move from simple projects to more complex projects and that drives additional learning — as you get more ambitious, you’ve got to learn more," Siegel adds.
Since they’re meant to encourage experimentation, there are few limits on what you can use the MakerSpace’s printers to create. Custom cell phone cases are a popular first project, Siegel says. But many on campus are putting the devices to educational use too.
For their senior design projects, students majoring in biomedical engineering partner with local physicians to identify novel treatment tools. These students have increasingly used 3-D printing to create quick mock-ups, says Professor Eric Kennedy, biomedical engineering.
"We can show the physicians pictures and they can say, 'It should be about the size of a screwdriver.' " Kennedy says. "But to actually print the part, hand it to a doctor and say, 'How does this feel? Do you want to hold it a different way?' That’s been really valuable."
But despite its possibilities, 3-D printing has drawbacks, he adds. "It’s new and novel, like the new app you get on your phone that you want to use for everything. The danger is becoming too reliant on it.”
Kennedy recalls several instances of senior design project teams engineering and printing their own plastic, less-refined versions of items that are otherwise readily available. One team, for instance, needed a clamp for its capstone project: an emergency tourniquet for battlefield use. The students reverse engineered and printed an Irwin Quick Grip clamp.
"If you’re trying to print a Quick Grip, why not just go get a Quick Grip?" he asks. Kennedy sees that example as a valuable lesson: get too used to a technology and it can influence the way you think, for better or worse. Meiser, however, has a different take.
He has made art and sculpture with computer-aided design software for the better part of a decade and recently began experimenting with 3-D printing. Meiser printed the head of an animatronic vulture he created with Professor Steve Shooter, mechanical engineering, and, with Siegel, he has begun translating 3-D prints into metal using the lost-wax method — combining a millennia-old technology with an emerging one. Next fall, Meiser will introduce this technique and others in a new digital-fabrication art course.
Meiser says designing 3-D forms on the computer has changed the way he creates in the studio, encouraging him to think in the keyboard commands Ctrl+C, V, X and Z — the shortcuts for copy, paste, cut and undo.
“If I’m working with physical materials in the sculpture studio and I make a mistake, sometimes I actually think, 'Undo,' " he says. "You can’t ‘undo’ things so easily in the real world. Sometimes you have wasted material or make a mistake that requires a lot of work to correct. It’s really empowering to design in the digital space because you can quickly iterate without worrying so much about failure. This ability to freely experiment with outlandish ideas helps us produce innovative results."
What has enabled the spread of 3-D printing technology at Bucknell and elsewhere is not that the technology is new, for it’s not as new as it may seem, nor as complicated. The technology has existed at Bucknell for two decades, since the Department of Mechanical Engineering purchased its first 3-D printer, a highly precise machine made by Stratasys that’s still used today. It has simply become much cheaper to access.
The drastic drop in prices has been almost laughable to watch, says Pratt, who, through several internships, has helped Ohio-based MakerGear refine its printer from a tricky-to-assemble kit to a plug-and-play desktop unit. He points to perhaps the most captivating to watch of the tools at the 7th Street Studio MakerSpace, a stereolithography printer, which uses a laser to solidify points within a pool of liquid resin, lifting a formed object layer by layer from the pool.
"That technology didn’t exist as something you could buy for less than a quarter-million dollars three years ago," Pratt says. "The machine in there is $1,500. That’s just one example."
That price drop has enabled faculty throughout the University to experiment with the devices and introduce them to students. Six printers have been purchased in the past year, Vigeant says, each for less than $1,000.
In fact, there are now so many printers on campus Vigeant has lost count. She tallies 15 owned by engineering departments, four in the 7th Street Studio and two in the Department of Art & Art History. Not included in that number is Ernie, an orange M3D Micro printer sitting atop Vigeant’s desk. The cost: about $350.
"It gets to a point where it’s not capital equipment anymore," she says. "It’s not an investment; it’s, 'This would be useful.'"
It’s clearly a price worth paying for training future engineers. The technology has been embraced by the biomedical engineering community, here and at large, where it’s already used to create custom-fit prosthetics. Someday soon printed medical devices could also mimic the body by changing material properties as they are printed, gradually morphing from hard to rubbery — a feature with huge implications for surgically implanted devices such as artificial heart valves. Within a few decades, Kennedy says, doctors might transplant organs grown from patients’ own cells, seeded to propagate in 3-D printed scaffolds.
The technology could disrupt traditional machining, warehousing and logistics operations too, adds Siegel, if it evolves to print metal more reliably and quickly. What does it mean, for instance, when auto-parts suppliers no longer need to keep warehouses full of replacement parts but can print to order?
But Vigeant also sees a more widespread ripple effect that extends beyond the drafting room, production floor and clinic. She can imagine a day when three-dimensional objects become just as pervasive a medium as internet access has made images and videos.
"A way to think about it is in terms of communication," she says. "We have had students practice communicating through writing for a long time and we have a few classes where we ask students to communicate visually or kinesthetically. My hope is that when the way you’re trying to express yourself works best as an item, you just go make it."