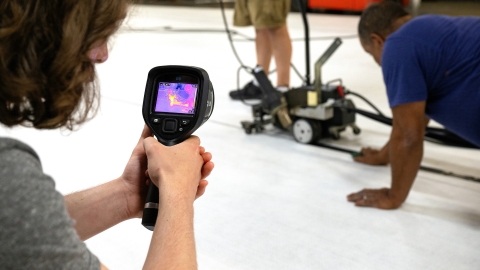
Manufacturing PA Grant to Fund Bucknell Engineering Project with Resilite
July 27, 2023
As part of a senior design project, Joe Carey '24 uses an infrared camera to collect data that will be used to help Resilite manufacture its Zip Mat. Photo by Emily Paine, Communications
Resilite Sports Products in Northumberland, Pa., is the world's leading producer of wrestling mats, and $3.5 million of its annual sales come from its Zip Mat product, which features a polyethylene ‘Zip’ to connect the six pieces of the mat together.
But there's a problem — the machine Resilite uses to attach the polyethylene ‘Zip’ connector to the vinyl mat surface is no longer produced by its manufacturer. That's why the company is now partnering with Bucknell University's College of Engineering on a project, funded by nearly $70,000 from a Manufacturing PA initiative grant, to have senior engineering students help design, manufacture and commission a new machine for the process.
"We're producing our Zip Mats for now, but the longevity of the machine is what we're concerned about," says Jenn Gilbert DeArmitt, Resilite Sports Products president. "Partnering with Bucknell, we're going to learn a lot. It's an awesome opportunity to engage with the community and learn even more about our product."
The Perfect Project
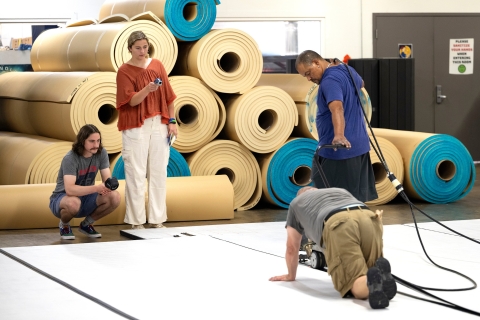
Joe Carey ’24 and Hunter Vestal ’24 gather research data as Resilite's Jose Correa-Gomez (standing) and Ryan Herman weld a Zip Mat. Photo by Emily Paine, Communications
Professor Craig Beal '05, mechanical engineering, the project's faculty adviser, has had two mechanical engineering students — Joe Carey '24 and Hunter Vestal '24 — gathering baseline research measurements this summer on both the machine and the process. It represents a perfect senior design project for Bucknell engineering students.
"From the student side, it's phenomenal," Beal says. "Students learn a lot of things in class and we hope they can solve problems and apply what they've learned. The students who are already working on the project just learned about heat transfer in the classroom, and they sat down recently and calculated the heat transfer required in this process. They're really just jumping in with both feet to attack this problem, which they'd never seen before."
They may not have seen the problem, but Carey was a wrestler at Camp Hill High School and saw the Resilite logo on his mats. He never knew he'd be working with that company as a student to solve a production problem.
"It's crazy to know that I'm involved in something so big [$3.5 million in annual sales]," Carey says. "I'm just using the technical knowledge that I've gained through school to contribute to this company, so it's really a cool experience."
Designed to Improve Efficiency
The new machine will be designed to both improve the speed of the process and reduce the physical strain on the Resilite operators. The Bucknell students have been thoroughly studying the plastic welding process this summer.
"My role in this project is defining exactly what parameters we need to hit to make a successful machine — so finding out what temperature we need to hit to get the machine to run at the speed we want in order to make it as efficient as possible," Vestal says. "And doing it as a student is just a great experience — we are seeing things go from concept to construction to actual use."
"It's a bit different than some senior design projects because they have an existing machine that functions to some extent, so we don't want to reinvent the wheel. But may want to see if there's a better way to do it," Beal says. "Welding mats is certainly a different material with its own complexities."
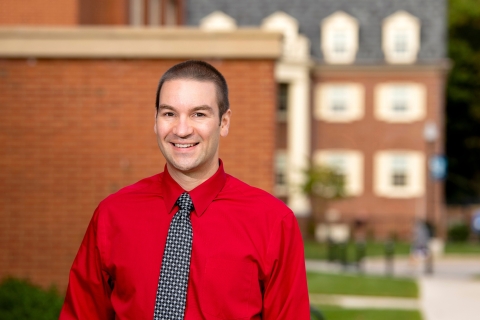
Professor Craig Beal ’05, mechanical engineering. Photo by Emily Paine, Communications
The manufacturing challenge also made it a perfect project for a grant from the Shapiro Administration's Manufacturing PA Innovation Program, which fosters collaboration between Pennsylvania universities and manufacturers. This Department of Community and Economic Development program awarded $2.1 million in grants to 31 projects in April. Bucknell Small Business Development Center Director Steve Stumbris and Innovation Engineering Manager Ian Proud worked with Resilite and the University on the application.
Beal says two additional senior engineering students will join Carey and Vestal on the senior design project this fall. The group will work with Resilite throughout the academic year with the goal of having a working machine by the end of the year.